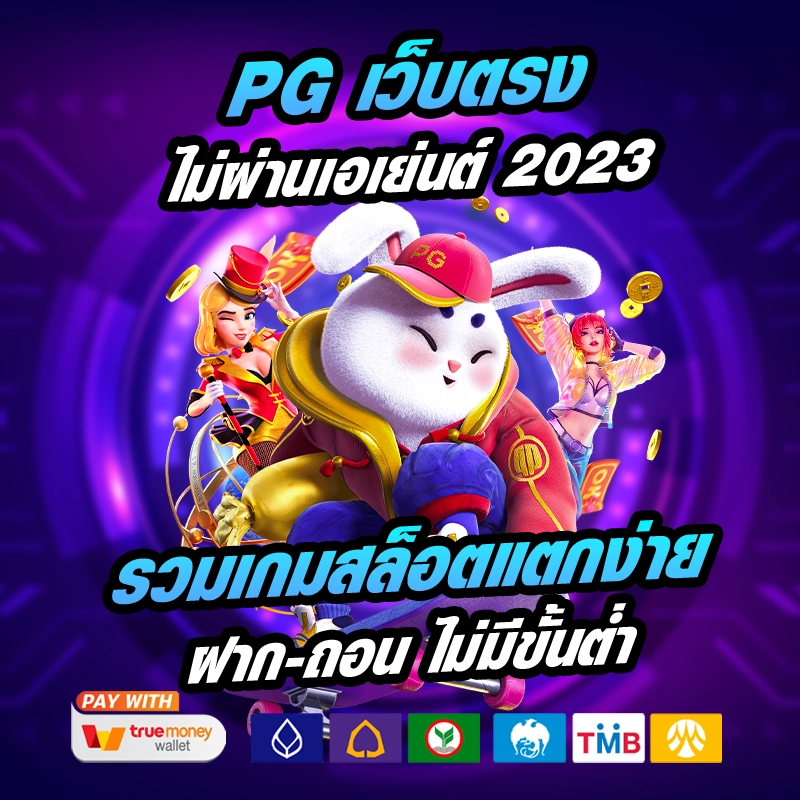
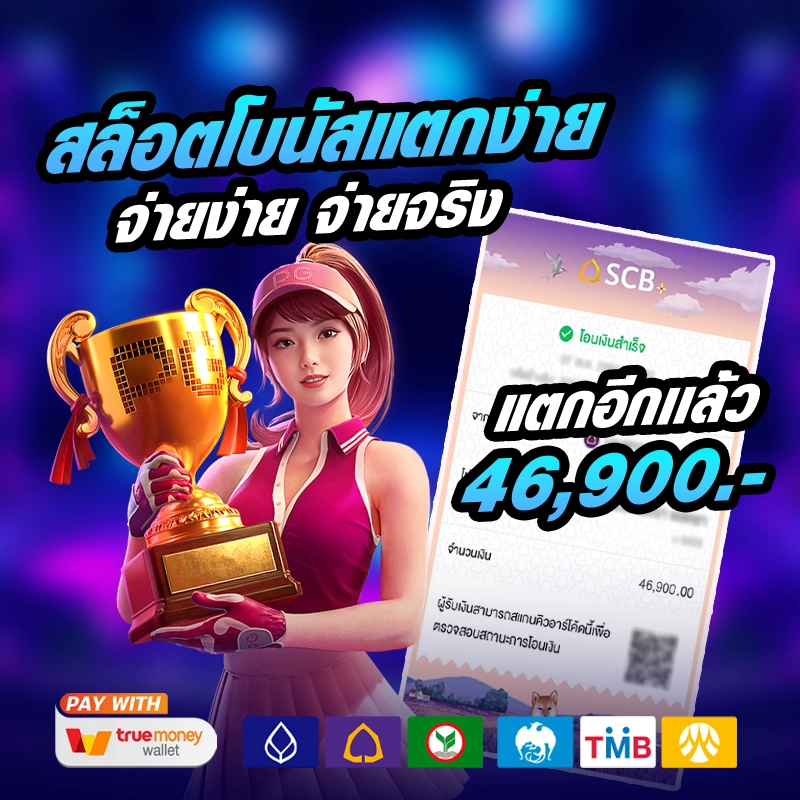
PG SLOT สล็อตเว็บตรง เว็บตรงไม่ผ่านเอเย่นต์ ไม่มีขั้นต่ำ แตกหนัก แตกง่าย
PG Slot สล็อตเว็บตรง ค่ายเกมมาแรงที่สุดในตอนนี้ สัมผัสประสบการณ์สุดตื่นเต้น ของการเล่นเกมสล็อตแตกง่าย แตกจริงกับ PG ด้วยแพลตฟอร์มเว็บสล็อตออนไลน์ ที่ดีที่สุด ออกแบบมาเพื่อแตกรางวัลง่าย ชนะเร็ว ช่วยให้รับเงินกำไรได้ทุกวัน เป็นค่ายสล็อตออนไลน์ที่ดีที่สุด มีเกมสล็อต pg slotใหม่ล่าสุด ให้เลือกจำนวนมาก เพื่อตอบโจทย์ความต้องการของนักพนันทุกคน ด้วยประสบการณ์เดิมพันระดับมืออาชีพ สล็อต pg เว็บตรง แตกหนัก และให้บริการระดับโลกคุณจึงสามารถไว้วางใจได้ เล่นเกม สล็อต PG รับประกันแจ็คพอตแตกหนัก และการชนะตัวคูณมหาศาล มีเกมเว็บสล็อต Pg ทั้งหมดคุณภาพสูงที่ออกแบบสล็อตpgแท้ มาเพื่อมอบความบันเทิงสูงสุด ให้กับผู้ที่ชื่นชอบเกม PG ทุกคน มอบประสบการณ์ที่ยอดเยี่ยมและเล่น Slot PG ไม่มีขั้นต่ำ ได้ต่อเนื่อง บนรวบรวมเกมสล็อตพีจี เล่นเกม สล็อตเว็บตรง ไม่ผ่านเอเย่นต์ ล่าสุด 2023 ได้เลย
PG SLOT สล็อตเว็บตรง เกมสล็อตออนไลน์ อันดับ 1 สมัครเว็บตรง ไม่ผ่านเอเย่นต์ ไม่มีขั้นต่ำ
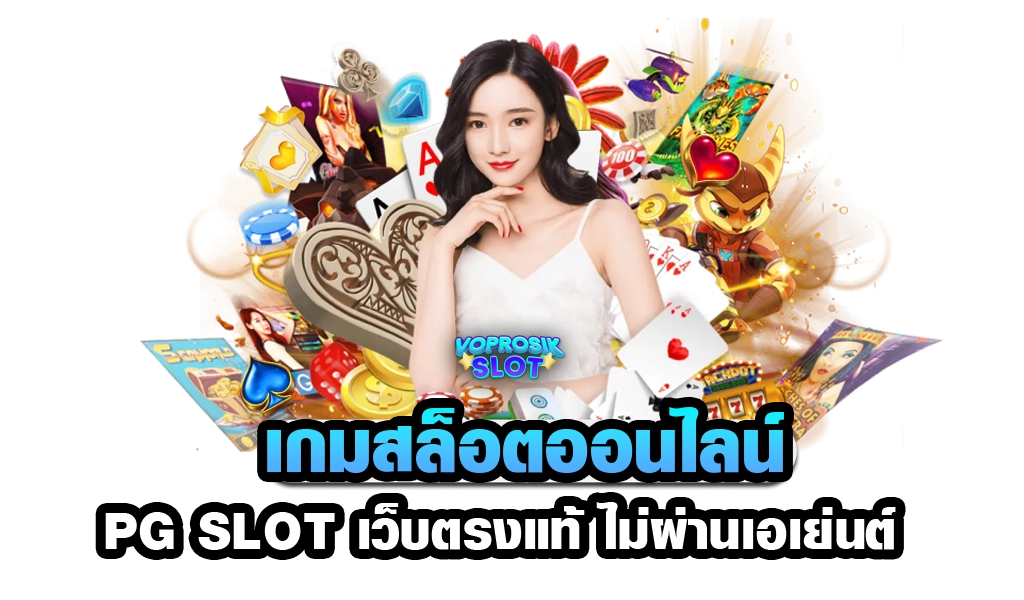
ขอแนะนำสุดยอดเว็บสล็อตออนไลน์ อันดับ 1 ที่ให้บริการเกมสล็อต Pg ที่มีชื่อเสียง ให้แพลตฟอร์มระดับโลก เป็นตัวเลือกอันดับต้น ๆ สำหรับคุณ ช่วยให้เข้าถึงการเล่น Pg slot สล็อตเว็บตรง ได้โดยตรง บนเว็บที่มีคุณภาพ โดยไม่ต้องผ่านเอเย่นต์ ให้รูปแบบเกมที่ทันสมัยและเล่นได้ปลอดภัย ช่วยให้มั่นใจต่อการชนะเดิมพัน รับประสบการณ์เล่นเกมสล็อตที่ราบรื่นและต่อเนื่องทั้งวัน เล่นสล็อต pg เว็บตรง ไม่ผ่านเอเย่นต์ สนุกได้จากทุกอุปกรณ์ และรองรับทั้งระบบ iOS และ Android มีระบบเกมสล็อตที่ดีที่สุด เกม PGSLOT จะดึงดูดใจได้ดีด้วยสีสันที่สดใสและกราฟิกที่น่าทึ่ง ช่วยเพิ่มความเพลิดเพลินในการเล่นเกมเต็มที่ทุกเกมที่นำเสนอโดย PGSLOT รับประกันประสบการณ์ที่น่าตื่นเต้นและให้ผลกำไรดีเยี่ยม มีคุณสมบัติเฉพาะที่ออกแบบมาเพื่อสร้างความตื่นเต้น และมีศักยภาพในการสร้างรายได้แบบไร้ขีดจำกัด เว็บสล็อต pg เว็บตรง ค่าย ใหญ่แห่งนี้ จึงนำเสนอเกมสล็อตพีจี ที่ถูกคัดสรรมาเป็นอย่างดี เพื่อให้มั่นใจถึงการเล่นเกมที่แท้จริง และเกมมีความสมจริงมาก ไว้วางใจได้ ให้การพัฒนาและปรับปรุงระบบเกมสล็อตเว็บตรง ไม่ผ่านเอเย่นต์อย่างต่อเนื่อง เพื่อรองรับการเล่นเกมสล็อต pg มาใหม่ล่าสุด เพียงเข้ามาสมัครสมาชิกตอนนี้ คุณจะได้ประสบการณ์เล่นเกมสล็อตขั้นสุดยอด ที่พร้อมแตกรางวัลใหญ่แบบจัดเต็ม
เกมสล็อต PG SLOT ยอดนิยม สล็อต pg ค่ายใหม่ เล่นสล็อตออนไลน์ เว็บตรง ได้เงินจริง
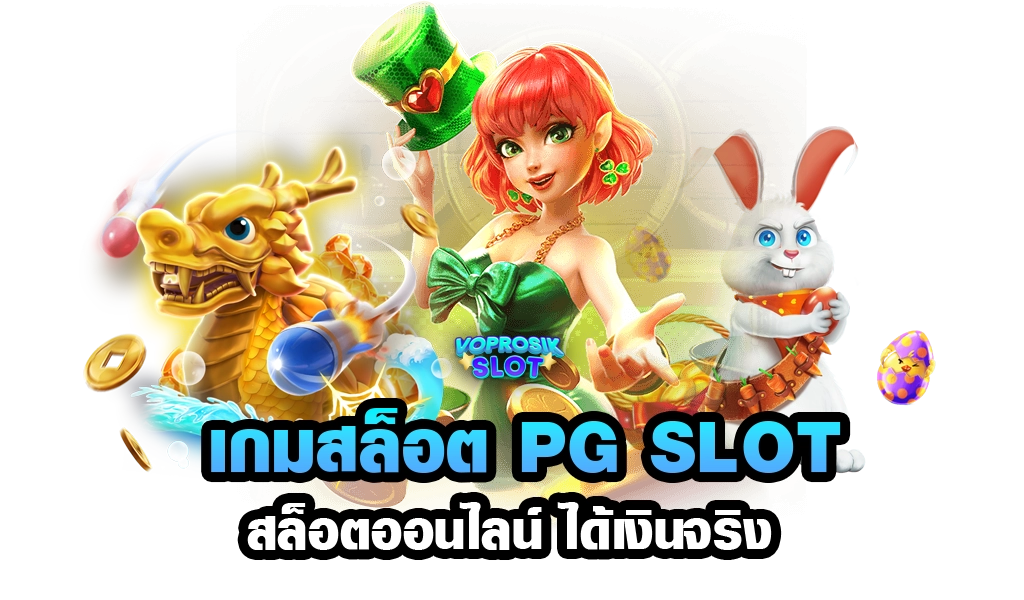
สำหรับผู้ที่ชื่นชอบการเล่นสล็อตออนไลน์ ได้เงินจริง PG SLOT คือ ตัวเลือกที่สมบูรณ์แบบที่สุด เพราะเป็นผู้ให้บริการเกมสล็อตค่ายยอดฮิต PGSLOT ที่มีเกมสล็อตหลากหลายและแตกโบนัสบ่อยครั้ง เป็นผู้ให้บริการเกมสล็อตที่ได้รับความนิยมสูงสุด สามารถนำเสนอเกมสล็อตยอดนิยม บนเว็บตรงได้อย่างยอดเยี่ยม โดยทางเว็บจะคัดสรรเฉพาะเกมสล็อตที่ดีที่สุด และบันเทิงขั้นสุด ที่ให้การแตกรางวัลดีจริงมาให้บริการ มีเกมให้เลือกเล่นมากกว่า 100 เกมขึ้นไป อัพเดตเกมใหม่อย่างต่อเนื่อง จากผู้ให้บริการเกม PGSLOT ที่มีชื่อเสียง สัมผัสประสบการณ์ความตื่นเต้น ในการเล่นเกมสล็อตใหม่ล่าสุด จาก สล็อต pg ค่ายใหม่ แตกหนัก อย่างมั่นใจ ให้ผลตอบแทนสูงแน่นอนนอกจากนี้ยังมีเกมสล็อตออนไลน์ที่ดีที่สุดจาก PG SLOT สล็อตเว็บตรง อีกหลายสไตล์ หลายรูปแบบ พร้อมครองใจผู้เล่นมาอย่างยาวนาน ผ่านการพัฒนามาใหม่ให้เล่นอย่างจุใจ ชนะง่าย และให้รางวัลแจ็คพอตบ่อยครั้ง คุณสามารถเพลิดเพลินกับเกมสล็อตยิงปลา PGSlot ที่จะรับประกันประสบการณ์น่าตื่นเต้นและสนุกเต็มที่ พร้อมใช้เกมทดลองเล่นสล็อตพีจี ได้ฟรี! เพื่อเพิ่มความมั่นใจต่อการเดิมพันสล็อตเว็บตรงจริง ช่วยให้คุณเล่นด้วยเงินจริงแล้วแตกรางวัลอย่างรวดเร็ว ซึ่งบริการเกมสล็อต pg แตกง่ายบนเว็บตรงจะชนะได้ง่าย และมีให้เล่นต่อเนื่อง ตลอด 24 ชั่วโมง
PG Slot แตกง่าย แตกบ่อย เกมสล็อตดีที่สุดของปี 2023 เกมสล็อตเว็บตรง pg มาแรง
สำหรับผู้ที่สนใจจะเล่นเกมสล็อต pg แนะนำให้คนได้รู้จักกับเกมรุ่นใหม่ล่าสุดของปี 2023 ที่ขึ้นชื่อในเรื่องของแจ็คพอตแตกง่ายและสล็อตพีจีให้ตัวคูณที่น่าสนใจ ดังต่อไปนี้
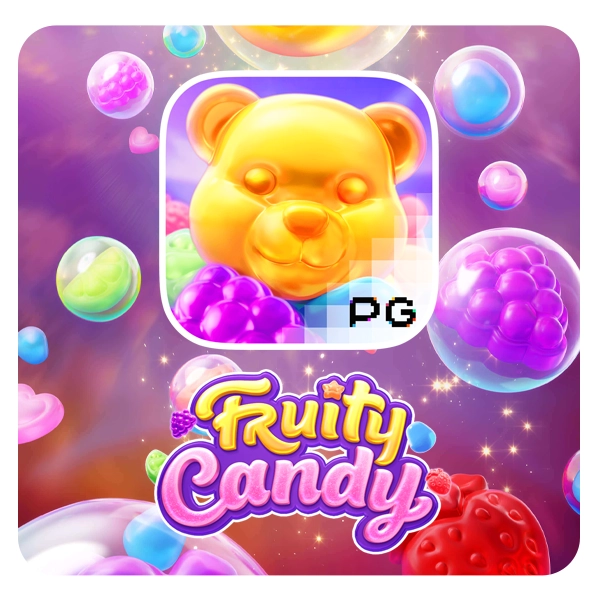
1. Fruity Candy
เกมขนมหวานที่มาในสไตล์แคนดี้ เป็นเกมใหม่ล่าสุดของค่าย Slot PG สล็อตเว็บตรง ที่ให้อัตราการคูณสูงสุดถึง 10,000 เท่า พร้อมให้เกมทดลองเล่นที่คุณสามารถเข้าไปตรวจสอบได้ จากเว็บตรงไม่ผ่านเอเย่นต์ ที่จะทำให้คุณเข้าถึงตัวเกมได้ง่ายมากขึ้น โดยเป็นเกมสล็อตวิดีโอ 3D ให้ค่า RTP 96.75% ทั้งยังมีฟีเจอร์ตัวคูณเหนือวงล้อ ที่ไม่ว่าคุณจะหมุนเกมปกติหรือเกมฟรี จะรับอัตราการคูณเพิ่มได้ทั้งหมด ให้การหมุนฟรีเริ่มต้น 10 ครั้ง และให้อัตราการคูณสูงสุด ในช่วงการหมุนปกติ 5 เท่า จึงเป็นเกมที่สามารถแตกรางวัลได้เรื่อย ๆ ไปตลอดทั้งการหมุน
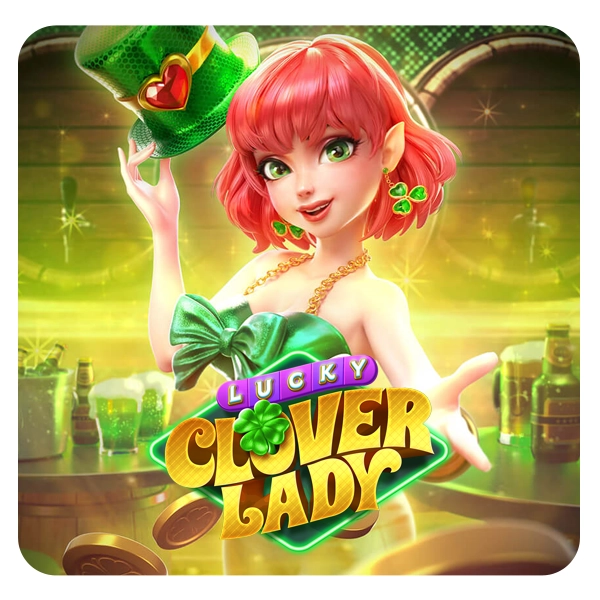
2. Lucky Clover Lady
ตื่นเต้นไปกับการผจญภัย และรับความโชคดีจาก Lucky Clover Lady ที่มาพร้อมกับสีเขียวเหนี่ยวทรัพย์ โดยเป็นเกมสล็อตวิดีโอ 3D แบบ 5 วงล้อ 6 แถว ที่ให้ค่า RTP 96.77% เลยทีเดียว การชนะเดิมพันสูงสุด ให้อัตราการคูณ 7,500 เท่า พร้อมให้สัญลักษณ์สำคัญที่จะสามารถพาคุณเข้าสู่รางวัลใหญ่ อย่าง Super Mega Win ได้ สัญลักษณ์พิเศษจะมีถึง 2 รูปแบบ และทำให้คุณรับอัตราการจ่ายเริ่มต้นตั้งแต่ 50-100 เท่า ไปจนถึง 100,000 เท่า ถือเป็นเกมสล็อต pg ใหม่ล่าสุด 2023 ที่สามารถให้การแตกรางวัลได้แบบรัว ๆ ด้วยรูปแบบของการระเบิดรางวัลอีกด้วย
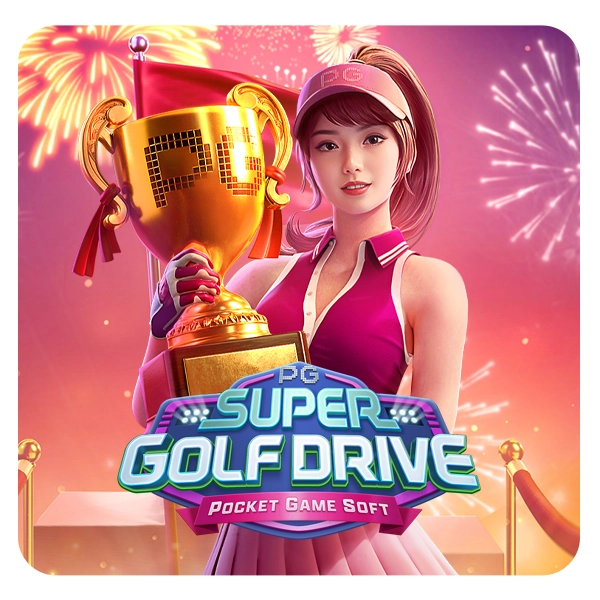
3. Super Golf Drive
เกมสล็อตสายกีฬา ให้ภาพสวยคมชัด และมาใหม่ล่าสุดของค่าย PG Slot คือ Super Golf Drive ที่นำมาจากเรื่องราวจริง ของนักกอล์ฟสาวคนดังที่มีฝีมือที่สุด และได้รับรางวัลระดับโลก อย่างลีโอ ดีเกล เป็นเกมสล็อตแบบ 6 วงล้อ 6 แถว ที่ให้อัตราการคูณเงินรางวัลสูงสุด 8,000 เท่า มีค่า RTP 96.78% ให้การแจกฟรีสปินสูงสุดถึง 10 ครั้ง มีสัญลักษณ์สำคัญหลากหลายรูปแบบ ที่จะพาคุณเข้าสู่การแตกรางวัลใหญ่ ได้แบบง่าย ๆ และให้อัตราการคูณของสัญลักษณ์ทั่วไป ตั้งแต่ 3 เท่า ไปจนถึง 30 เท่า เรียกได้ว่าเป็นหนึ่งในเกมที่สามารถให้ตัวคูณแบบสุดปังเลยทีเดียว
เว็บตรง PG Slot เล่นเกมสล็อตฟรี เว็บตรงไม่ผ่านเอเย่นต์ เว็บแท้ล่าสุด
เข้ามาร่วมสนุกด้วยการสมัครสมาชิก กับเว็บตรงไม่ผ่านเอเย่นต์ แล้วเข้ามาเล่นเกมของ Slot PG ค่ายเกมสล็อตแตกง่ายวันนี้ คุณจะสามารถรับโบนัสได้แบบไม่จำกัด เล่นแล้วแตกรางวัลโบนัสได้รัว ๆ ไม่ว่าจะเป็นเกมรุ่นใหม่ล่าสุด หรือเกมเก่าของค่าย PG เมื่อเข้ามาเล่นแล้วคุณจะแตกรางวัลแบบไร้ขีดจำกัด ให้ความสนุก ความท้าทาย และความตื่นเต้น ด้วยการสนับสนุนของทางเว็บตรง สมัครเว็บสล็อต ที่ดีที่สุด ที่จะเป็นการให้โปรโมชั่นสุดคุ้ม รับแล้วเงื่อนไขไม่ยุ่งยาก ใช้งานง่าย สล็อตเว็บตรง ไม่ผ่านเอเย่นต์ ไม่มีขั้นต่ำ มีข้อเสนอที่น่าสนใจทำให้การจบยอดเทิร์นโบนัสสล็อตเครดิตฟรีไม่ใช่เรื่องยาก ถอนเงินออกได้อย่างรวดเร็ว ทั้งยังมีโปรให้คุณเลือกอย่างหลากหลาย โปรสล็อต ฝาก 100 รับ 100 ที่ถูกทำขึ้นมาเพื่อให้เหมาะสมกับเกมสล็อต แต่ละรูปแบบของค่าย PG เมื่อนำไปใช้แล้วรับรองการแตกรางวัลได้จุใจ พร้อมให้ทุกระบบ ทุกด้าน บริการที่ง่ายต่อความเข้าใจเป็นอย่างมาก ไม่ทำให้คุณต้องสับสน การสมัครสมาชิกเริ่มต้นเพียงแค่ 1 นาที รับการฝาก-ถอนเงิน หลังการชนะเดิมพัน ใช้ระยะเวลาเริ่มต้นเพียงแค่ 5-10 วินาทีเท่านั้น
สมัครเล่นเกมสล็อต PG เว็บตรง ได้เงินจริง แตกง่าย ถอนได้ไม่อั้น 2023
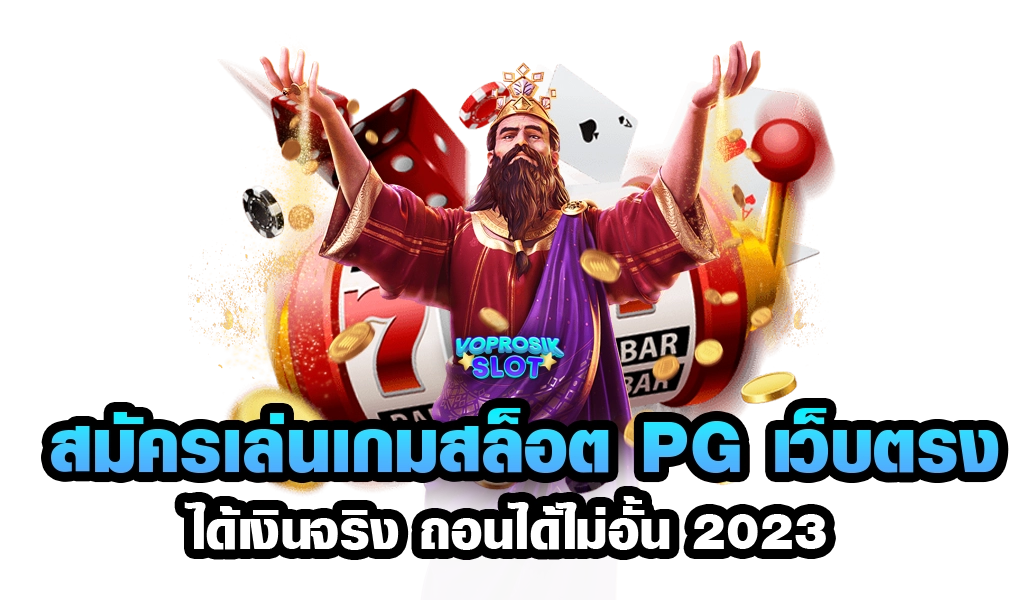
เมื่อคุณต้องการสมัครสมาชิกกับสล็อตเว็บตรง ที่ให้บริการเกมของค่าย PG ได้ดีที่สุด แนะนำให้คุณได้สัมผัสถึงข้อดีของงานบริการจากเว็บตรง ที่คุณจะไว้วางใจได้ ก่อนการสมัครสมาชิกจริง คือ
- มีความน่าเชื่อถือสูง ด้วยการเป็นเว็บสล็อตตรง ไม่ดำเนินการผ่านคนกลาง และมีบริการเกมของ PG SLOT เว็บตรง จำนวนมาก เข้าเล่นแล้วไม่มีเสียหาย แตกรางวัลได้ดีจริง
- เมื่อเปิดเข้าสู่เกม PGSLOT แล้ว จะสัมผัสได้ถึงระบบภายในที่ใช้งานง่าย การแตกรางวัลมาเรื่อย ๆ และแตกได้ทุกรางวัลเกมสล็อต pg มีโอกาสชนะได้ค่อนข้างสูง
- เล่นเกม PG สล็อตแตกหนัก จะให้การแตกตัวคูณกับแจ็คพอตที่มาเรื่อย ๆ ตลอดทั้งเกม เมื่อได้เข้าเล่นเกมแล้ว จะรู้ถึงการเป็น PG Slot แตกหนัก แตกจริง ได้เต็มทุกยอด พร้อมด้วยวิธีการเล่นภายในเกมที่ไม่มีความซับซ้อนเลยแม้แต่น้อย
- ธีมเกมมีความแปลกใหม่ ไม่เหมือนใคร ให้ความหลากหลายสูง การเล่นของคุณจึงไม่น่าเบื่อและไม่ซ้ำอยู่แต่เกมเดิม ๆ แน่นอน
- ร่วมสนุกไปกับเกมสล็อตของเว็บตรง ได้จากทุกที่ทุกเวลา บนระบบของมือถือสมาร์ทโฟนและแท็บเล็ต ที่ให้การรองรับต่อทั้ง Android และ iOS
- เล่นเกมได้ต่อเนื่องตลอดทั้งวัน และ 24 ชั่วโมง ไม่มีการปิดปรับปรุง และไม่มีวันหยุด ให้บริการจากทีมงานมืออาชีพ ที่จะทำให้คุณได้รับความช่วยเหลือไปตลอด
- ลงทุนมาก กำไรสูง แต่ถ้าทุนน้อยก็สามารถชนะเดิมพัน แล้วรับเงินรางวัลแบบสะสม จนทำให้คุณได้เงินรางวัลที่ถูกใจแน่นอน
- ให้การฝากขั้นต่ำน้อย ไม่ต้องกังวล ไม่สร้างแรงกดดันใด ๆ ทั้งสิ้น พร้อมทำให้คุณใช้บริการสล็อตทรูวอเลท ที่ให้การฝาก-ถอนแบบไม่มีขั้นต่ำ ไม่ว่าจะชนะเดิมพันด้วยเงินเท่าไหร่ ถอนออกได้ทันที
- การสมัครสมาชิก PG SLOT สล็อตเว็บตรง และการใช้งานระบบต่าง ๆ บนเว็บจะฟรีทั้งหมด รวมไปถึงการรับโปรโมชั่น และการถอนเงินออก ไม่จำเป็นต้องเสียค่าธรรมเนียมหรือค่าเปอร์เซ็นต์
- การรับโปรโมชั่น จบยอดเทิร์นเร็ว เพียงแค่คุณทำตามเงื่อนไขของทางเว็บให้เรียบร้อย คุณจะสามารถหลุดยอดเทิร์นแล้วรับเงินจริงได้ทันที
- มีการจัดทำโปรโมชั่นสำหรับสมาชิกใหม่ เพื่อเป็นการสร้างความมั่นใจต่อผู้เล่นเกมมากขึ้น
- สมาชิกดั้งเดิม ทางเว็บจะมีโปรโมชั่น และกิจกรรมพิเศษต่าง ๆ ที่อัพเดทผ่านหน้าเว็บทางเข้ากับเว็บหลักอยู่เสมอ เพียงแค่คุณติดตาม เชื่อว่าคุณจะสามารถรับโปรโมชั่น และเข้าไปใช้งานกิจกรรมพิเศษ พร้อมรับรางวัลได้อย่างมั่นใจ
เว็บสล็อต PG SLOT เว็บหลัก สมัครสล็อตเว็บตรง ไม่ผ่านเอเย่นต์ ไม่มีขั้นต่ำ ได้แล้ววันนี้
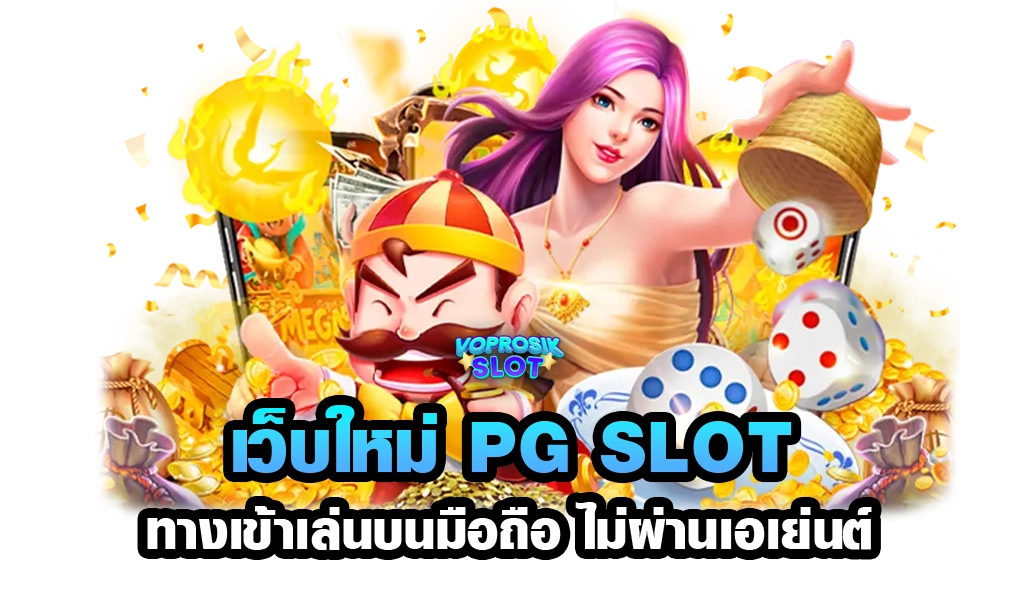
ถ้าพูดถึงค่ายเกมทางเลือกที่ได้รับความนิยมสูงสุด ต้องยกให้กับ PG SLOT สล็อตเว็บตรง เพราะเป็นหนึ่งในผู้ให้บริการเกม ที่มีคุณภาพสูง ได้การยอมรับจากนักพนันทั่วโลก เพราะพีจีสล็อตมาเป็นอันดับ 1 ของวงการสล็อตออนไลน์ภายในประเทศไทย เหมาะสำหรับคนที่ชื่นชอบการเล่นเกมสล็อต ที่สามารถเล่นได้อย่างคล่องตัว ทั้งบนเครื่องคอมพิวเตอร์ PC มือถือสมาร์ทโฟนและแท็บเล็ต เพราะเป็นผู้ผลิตเกมที่มีความเด่นในด้านการผลิตเกมบนมือถือมีการจัดทำทุกส่วนของเกมออกมาให้เหมาะสมต่อการเล่น ช่วยเพิ่มอรรถรสความบันเทิงได้เป็นอย่างดี นอกจากนี้ยังมีให้บริการเฉพาะบนเว็บสล็อตตรง ไม่ผ่านเอเย่นต์ เท่านั้น คุณจึงมั่นใจได้เลยว่าการเล่นเกมของคุณ ไม่ว่าจะเป็นค่าย สล็อตพีจี ลิขสิทธิ์แท้ 100 % หรือค่ายใดก็ตาม เพียงแค่เลือกสมัครสมาชิกกับเว็บตรง คุณจะรับเงินอย่างมั่นใจ เล่นเกมไม่มีกดดัน ด้วยระบบฝาก-ถอนที่ให้ขั้นต่ำน้อยไปจนถึงไม่มีขั้นต่ำ และหลังการชนะเดิมพัน รับเงินได้ทันที
เลือกเล่น PG SLOT เว็บตรงใหม่ล่าสุด ฝาก-ถอน Auto แตกหนัก สล็อตเว็บตรง 100%
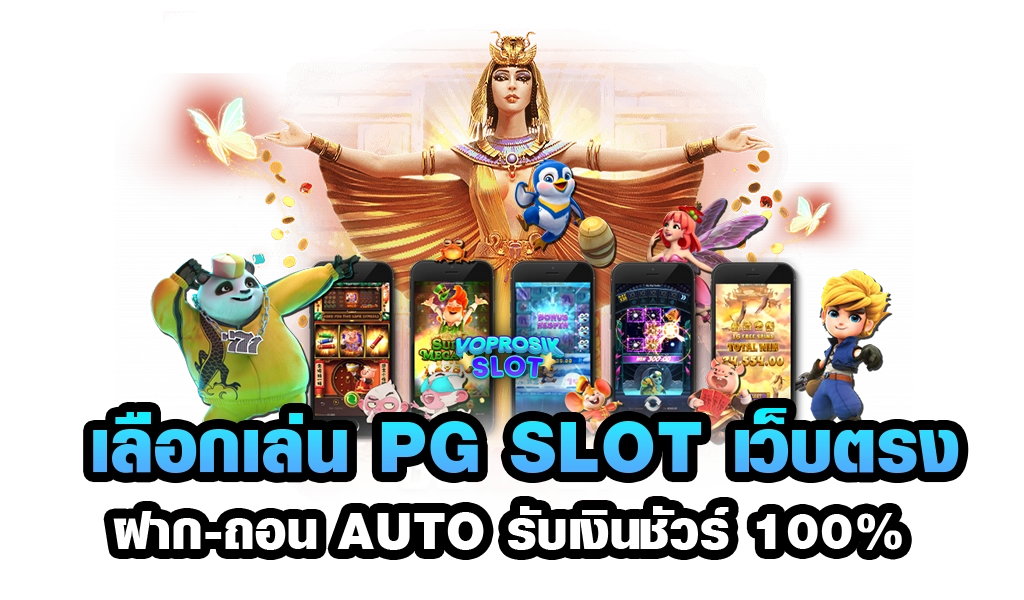
การเล่นเกมสล็อตออนไลน์ยุคนี้ ถ้าพูดถึงเกมที่สามารถแตกรางวัลได้ง่ายที่สุด คือ เกมของค่าย Pg slot สล็อตเว็บตรง เพราะเป็นผู้ผลิตและสร้างสรรค์เกม ในสไตล์เกมแตกกังวลง่าย ที่มาเป็นอันดับต้น ๆ ของโลก ทั้งยังถูกจัดให้เป็นผู้สร้างเกมสล็อตเจ้าแรก ๆ ที่ได้รับความนิยมสูงสุด ในด้านการเป็นเกมแตกรางวัลง่าย ให้ความรวดเร็วทันใจ ในการเข้ารางวัลต่าง ๆ ได้เป็นอย่างดี ดังนั้นจึงตอบคำถามได้อย่างชัดเจนว่าเกมของ PG Slot จะแตกง่ายจริงหรือไม่ ด้วยการเข้าไปทดลองเล่น และสัมผัสระบบต่าง ๆ ภายในเกมแบบไร้ขีดจำกัดด้วยตัวคุณเอง แล้วจะรู้ว่าค่ายเกมแห่งนี้ มีความโดดเด่นในหลากหลายด้าน ไม่ใช่แค่เพียงการทำให้เกมแตกรางวัลต่าง ๆ ออกมาได้ง่ายเท่านั้นเว็บสล็อตตรง ไม่ผ่านเอเย่นต์ มาพร้อมกับภาพกราฟิกสวยคมชัด ก่อนการจัดทำเป็นเกมออกมาให้เล่น จะมีการประเมินมาแล้วว่าต้องถูกใจผู้เล่นเกมโดยตรง การจัดทำภาพต่าง ๆ ออกมา มีรายละเอียดที่ยอดเยี่ยม รวมไปถึงเทคโนโลยีที่ใช้ร่วมกับตัวเกม มีความทันสมัยสูง และไม่ว่าวงการเกมคาสิโนออนไลน์ จะมีการผลิตนวัตกรรมใหม่ออกมา ค่าย PG จะถือเป็นเจ้าแรกที่นำมาสู่การจัดทำเกมแล้วโดดเด่นที่สุด พร้อมให้การผสมผสานธีมเกมที่เป็นเอกลักษณ์โซนยุโรปและโซนเอเชีย ได้อย่างน่าสนใจ จึงทำให้ค่าย PG สล็อตโดดเด่นและมีเอกลักษณ์เฉพาะตัว พร้อมดึงดูดความสนใจและความชื่นชอบของนักพนันไทย กับผู้เล่นเกมโซนเอเชียได้เป็นอย่างดี
ทางเข้าเล่นสล็อต PG แตกหนักกับ เว็บตรงไม่ผ่านเอเย่นต์ ฝากถอนไม่มีขั้นต่ำ 1 บาทก็ถอนได้
เข้ามาเพิ่มโอกาสการแตกรางวัลง่ายแบบจุใจ บริการสมัครสมาชิกกับเว็บตรง แล้วเลือกเล่นเกมจากค่าย PG Slot เพียงเท่านี้คุณจะสามารถรับเงินรางวัลที่ต้องการได้อย่างเต็มที่ เล่นเกมแล้วได้กำไรตรงตามเป้าหมายที่ต้องการแน่นอน พร้อมให้การสมัครสมาชิกเว็บสล็อตตรง และการใช้ระบบต่าง ๆ บนเว็บตรงที่ไม่ยุ่งยาก เข้าใจง่าย เป็นไปอย่างตรงไปตรงมา พร้อมทำให้คุณรับโอกาสของการสร้างเงินกำไรที่ดีได้ทุก ๆ วันแน่นอน ดังนั้นอย่ารอช้า! เลือกเว็บตรงที่คุณไว้ใจได้แล้วสมัครสมาชิกพร้อมตรงเข้าเล่นเกมของค่าย PG ได้เลย